Back to applications
DC-DC Converter for (H)EV
Gain up to +15% energy with ACS
Tackling key challenges of DC-DC converters
OEMs face the following challenges with DC-DC converter control systems:
- Achieving high efficiency all across the DC-DC operating range
- Achieving power density while maintaining compactness of the module
- Power module cost reduction
- Implementing a safe bidirectional power flow
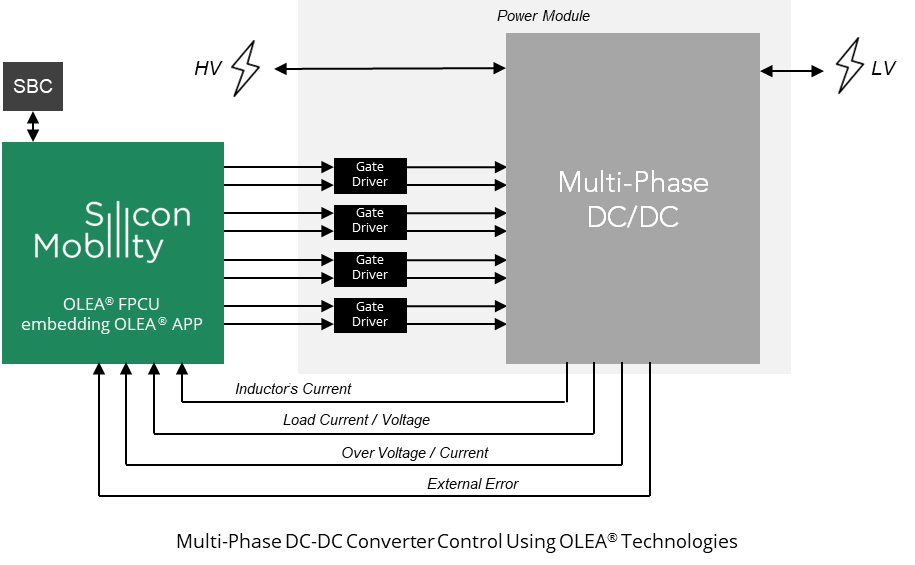
Our Solution for DC-DC Converter
We offer the following solutions to address the DC-DC converter control application:
- ACU U310 – A single chip solution for integrated powertrain domain control and energy management
- ACU T222 – Automotive qualified semiconductor solution with software libraries and development tools
- AC Composer – Model-based application development and calibration framework for ACU
- AC Lib – Rich collection of advanced software and control algorithms optimized for the ACU
- AC App DC-DC Application software integrating innovative algorithms delivering High Efficiency DC-DC control
Key Benefits
- Support 48V to +800V for HEV and EV
- Support any MOSFET, IGBT, SiC or GaN based inverters
- 100% Model based design accessible as source code
- Soft switching enabling a better transistor current rating for BOM reduction and for transistor down-sizing
- Cancellation of inductor current ripples and output current and voltage ripples
- Reduction of filtration requirements for Electromagnetic Interference (EMI)
- Up to 15% of energy gain over with reduction of switching and conduction losses in the power module all across the load operating points
- Up to 50% of transistor current rating increase
- Up to 50% BOM reduction on the required power transistor and passive components
- Up to 1MHz control enabling passive component size and weight reduction (power density improvement by a factor of 10)